It went like this: For two decades, hundreds of thousands of people entered and exited through the doors of one of the largest skyscrapers in New York City. Many of them were workers who rode up and down in the elevator, completely unaware that the building had critical, architecturally terrifying failure that had gone unnoticed. This type of situation has rarely occurred in the history of urban planning in large cities.
The (floor) plan. The story dates back to the early 20th century when St. Peter’s Lutheran Church stood on a lot on 53rd Street between Lexington Avenue and Third Avenue in Midtown Manhattan. By 1960, the church community was facing serious financial trouble, prompting the City Council to sell the land. Negotiations lasted for years. They weren’t easy because the church insisted on the creation of a new building separate from the block of apartments, where it could continue its activities.
Authorities ultimately gave the project the green light. Citibank commissioned Hugh Stubbins & Associates to design a skyscraper, while William LeMessurier was responsible for the engineering. The final project included a skyscraper, a church, a public space below street level, and landscaping.
The main focus of the project was the skyscraper, which was planned to have 46 floors. The architecture firm designed a facade with polished and anodized aluminum, giving it a distinct appearance from the rest of the city. Additionally, the architects incorporated rows of windows between the panels. The skyscraper design seemed straightforward, at least when compared to the complexity of the roof and base of the building.
The roof. The skyscraper was completed in 1977, and by then, it had become even bigger, with 59 floors and a total height of 915 feet. This architectural marvel stood out in the city skyline, with a colossal tower featuring a distinctive 45-degree inclined top.
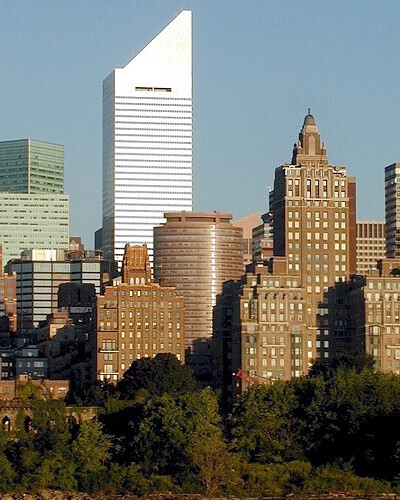
The top of the roof took the form of an isosceles triangle. Initially, there were plans to build terraces and apartments, but the architects eventually decided to install large solar panels. LeMessurier, a professor and graduate of the Massachusetts Institute of Technology, conducted a series of tests to evaluate their efficiency. He later discovered that the energy generated by the installation was insufficient. Consequently, he abandoned the idea of a small solar plant.
The four stilts. The building, the seventh-largest skyscraper on the planet at the time, had four large stilts. Those four gigantic pillars (112 feet each) were positioned at the center of each side of the base, rather than at the corners.
There was also a narrower central column which housed the building’s elevator benches and provided extra support. This design allowed for space to be used for a church under the northwest corner of the building. Despite its large size, the building was exceptionally “light,” weighing only 25,000 tons. For reference, the Empire State Building weighs 60,000 tons.
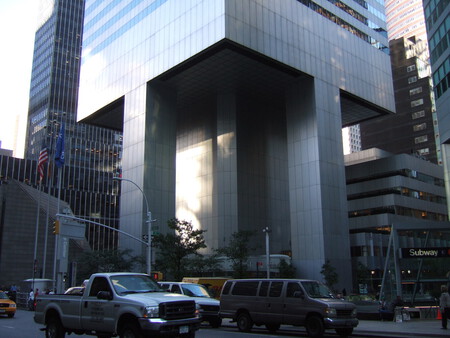
The bracing structure. The building’s base became an architectural icon due to the creation of unique, unobstructed corners. LeMessurier designed the skyscraper’s weight to be supported by an outer skeleton. This structure consisted of inverted chevron-shaped frames concealed behind the building’s facade. Interestingly, this design was visible from the inside. The elements weren’t fully welded but were instead fixed with bolted joints.
This steel frame was specifically designed to resist perpendicular winds. The engineers believed that other wind forces wouldn’t be a threat. Additionally, local regulations didn’t require the consideration of other winds in the building’s design.
TDM. The Citigroup Center was built with an important mechanism hidden in the upper floors known as a tuned mass damper (TDM). This TDM consisted of a 360-ton concrete sphere embedded in oil. When the building experienced ground vibrations or wind forces, the TDM would move in the opposite direction to counteract the building’s movement.
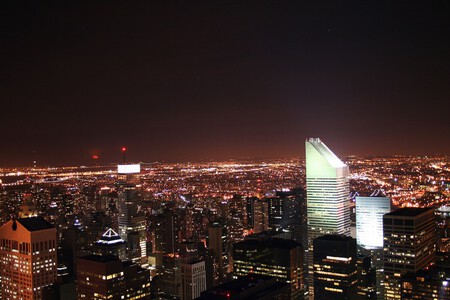
To balance this rocking motion, hydraulic arms supported the sphere. This innovative solution allowed the skyscraper to maintain its stability. According to LeMessurier, the TDM’s function was key in reducing the building’s sway by converting the kinetic energy of the sway into friction, effectively cutting the building’s sway in half.
First doubts. After the completion of the Citigroup Center in 1977, concerns arose about its structural integrity. Although New York City isn’t frequently affected by hurricanes, the possibility of high winds exceeding 60 mph every 50 years raised questions about the building’s ability to withstand such conditions, especially as the winds could come from different directions.
First call. A year later, bad news came for LeMessurier. An engineering student from Princeton University, Diane Hartley, contacted the building’s architect. She had studied the building’s construction for her architecture bachelor's thesis and had some technical questions regarding the skyscraper’s design. Hartley’s professor had raised doubts about the strength of a leaning skyscraper with its support columns positioned away from the corners.
Hartley performed wind load calculations for the building and found discrepancies when comparing them to LeMessurier’s calculations. When she asked for the exact load calculations for different types of wind, she only received data for perpendicular winds and assurances about the strength of the structure.
Additionally, LeMessurier informed her that the professor was clueless and that everything was in order. The building’s frame geometry and pillar positions were designed to withstand very strong winds, even from diagonal angles.
Second call and a fatal discovery. Soon after that, LeMessurier received a second wake-up call. It was another student, Lee DeCarolis from the architecture department of the New Jersey Institute of Technology in Newark. DeCarolis convinced LeMessurier to conduct a new calculation.
This was the first time the engineer started doubting his own project. After finishing the new calculation, LeMessurier was taken aback to discover that the maximum load on the steel triangles would exceed 40% when the winds blew diagonally. This meant that the bolts connecting the structures were even more overloaded, with up to a 160% increase in load at all connecting joints.
What had happened? LeMessurier was interested in the effects of an engineering change that was made during construction and had seemed correct at first. Originally, the numerous joints were supposed to be welded, but they ended up being secured with bolts instead. This change isn’t normally a big issue, but the design of the Citicorp Center was sensitive to diagonal winds, so the results of their calculations were very concerning.

A serious problem. To understand the seriousness of the problem, you should consider that the force of the wind on flat surfaces of a building, especially tall structures like skyscrapers, exerts significant pressure on the building’s base.
Although gravity plays a major role in holding the building together, it’s essential for the joints to be strong enough to withstand forces not countered by gravity. In this case, LeMessurier feared that the joints might not be strong enough for the task.
Searching for a solution. After staying indoors for a few days, the engineer reached out to lawyers and other experts to devise a plan to address the mistake. They confirmed that gusts exceeding 60 mph could potentially break the joints supporting the building’s foundation, resulting in a very serious structural failure.
Shortly thereafter, workers began repair work at night because there was no time to lose in the face of a possible catastrophe with unpredictable consequences. Meanwhile, life continued to function “normally” inside the skyscraper. The engineer’s plan was to reinforce the 200 bolted joints by welding 5.1 cm thick steel plates to cover the bolts.
In addition, experts were constantly checking the integrity of the columns and the entire skeleton. The architecture studio couldn’t afford even the slightest failure. The access to power sources of the concrete ball on the roof was secured. In case of a collapse, Manhattan had a plan, but it was never made public so no one would panic.
20 years passed in silence. The truth is that the reinforcement plan was finalized at the end of 1978, a year after the structural failure became known, but no one said anything. The case was uncovered in 1995 with a The New Yorker article describing what happened almost 20 years before, bringing to light, for the first time, the historic failure with which the skyscraper was erected.
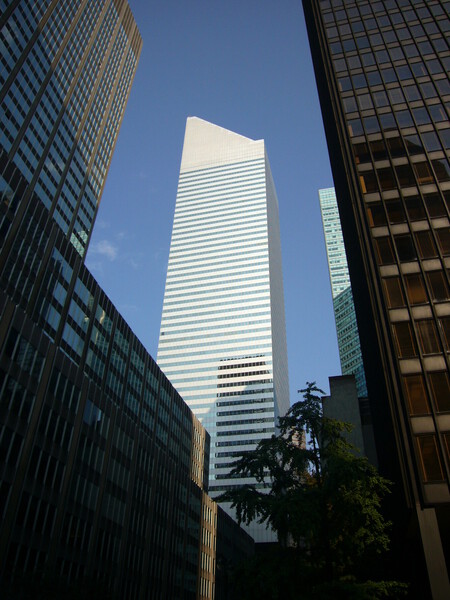
However, neither LeMessurier nor the architects and engineers of the Citigroup Center faced legal consequences for correcting their mistakes. The cost of the modifications amounted to several million dollars, which was covered by the company’s insurance.
Today, new calculations show that every few hundred years winds occur that can severely damage a building. We’ll never know what would’ve happened if they hadn’t repaired Citicorp, but we do know the name of the heroine who may have saved thousands of lives: Diane Hartley.
This article was written by Miguel Jorge and originally published in Spanish on Xataka.
Image | Andrew Moore | Elisa.rolle | Johan Burati | Trxr4kds | Max Hermus | Amar.raavi
Related | New $1.6 Billion Legends Tower in Oklahoma City Set to Be Tallest Skyscraper in U.S.