Brick has been an essential building material since 7000 B.C., when mud bricks were the norm. In 4000 B.C., ancient builders discovered that firing the bricks at high temperatures, rather than air-drying them, produced a more workable, transportable, and durable material. Along with concrete, brick remains a cornerstone of cities, and although less polluting than concrete, traditional brick production also releases carbon dioxide into the atmosphere.
Now, researchers have set out to change that and reinvent brick. The solution? A return to ancient techniques from 9,000 years ago. Well, sort of.
Reinventing the brick. In the quest to cut emissions, experts have found a way to reduce the carbon footprint of building materials. Not only is the production of bricks and concrete carbon-intensive, but steel manufacturing, which is also critical to construction, is a significant pollutant. For example, the Neom development project reportedly uses 20% of the world’s steel production, underscoring the need for greener alternatives. As such, researchers are exploring ways to cut concrete use, increase wood usage, and produce steel more sustainably.
The same is true for bricks. There are now concrete-alternative bricks that are stronger and more eco-friendly, staple bricks that require no concrete, wood bricks that capture carbon dioxide, and even next-generation terracotta bricks.
The magic formula. Add a new type of brick to this list of sustainable building materials. Tavs Jorgensen, a researcher at the University of the West of England in Bristol, has developed a method for creating sustainable adobe bricks that don’t require mortar. According to Dezeen, Jorgensen’s process involves stacking bricks in interlocking patterns that form strong bonds, thanks to an innovative brick shape.
The base material for the bricks is clay, but the key ingredient is hemp. Jorgensen and his team experimented with various shapes, clays, and fillers before settling on a mix of clay, water, and hemp, finding it provides strength when dry. The plant fibers act like steel does in reinforced concrete, adding durability.
Multi-purpose. Interestingly, the researchers designed two versions of these bricks to suit various environments and structures. For outdoor use or load-bearing structures, the “heavy” bricks are made from a mix of sand, clay, water, and barley straw as a binder. For “light” bricks, used in less demanding settings, the mix is simpler: two parts liquid clay to three parts reed from the woody core of the hemp plant.
3D printing. The video above highlights another essential component of these sustainable bricks: the mold. Traditionally, making adobe bricks is “complex” due to the labor and machinery required to shape them. However, Jorgensen’s team developed a series of 3D-printed molds that allow the bricks to take on unique shapes and complex geometries, simplifying the process.
Using these molds is akin to playing with Play-Doh, allowing for various patterns depending on the mold’s shape. “We wanted to explore some new design concepts with the cob brick dies, particularly ways of creating interlocking bricks to avoid the need to build with mortar, which is typically the weakness in clay brick constructions,” Jorgensen says. “The approach of using 3D-printed extrusion dies allowed for rapid and low-cost exploration of such ideas,” he added.
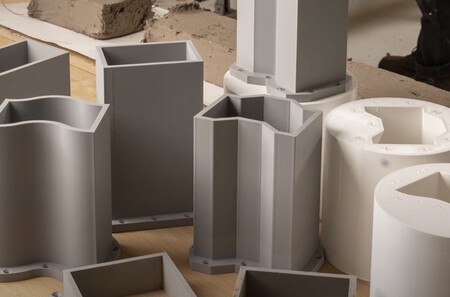
Unfired bricks. So, which part of the process is sustainable? Aside from the 3D molds, nearly everything else. The materials are eco-friendly, as the bricks are made from earth and straw and don’t require firing. As a result, carbon emissions are significantly lower than those of the current brick industry, which must burn clay and other minerals at temperatures above 662 degrees Fahrenheit.
According to Jorgensen, hemp fibers act as a “glue.” “The fibers bind the cob composite together, so firing is not necessary. Avoiding firing makes cob bricks an extremely low-carbon building material,” he explains.
Recirculation. In addition to being more sustainable, Jorgensen’s bricks are easy to build with and fully recyclable. Construction experts are exploring methods to recover building materials when structures are no longer useful. With these bricks, the goal would be to essentially melt down the building.
“Unfired cob bricks can also easily be returned to the raw state of the components—basically just earth and compostable fibers—so complete material circularity can be achieved with no waste at all,” Jorgensen states.
However, for innovations like this to be impactful, the construction industry must adopt them on a large scale.
Images | Dezeen (YouTube)
Related | New Biomaterial Achieves What Was Science Fiction Until Now: High-Quality Articular Cartilage Growth
Log in to leave a comment